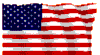


Earth Sheltered Green Homes
from Earthlog Custom Homes®
a Subsidiary of
Earthlog Equity Group®
[email protected]
Earthlog Equity Group® Partners with
Major Lending Group : Click here
Earthlog Custom Homes® Building Systems :
Standard use of Fiber Glass/Mix in our Concrete for all of Our Homes
& Commercial Structures.
Our System creates a concrete, steel reinforced structure that provides cost
effective, flexible, durable and aesthetic solutions for living with the environment.
Imagine a place with delightful sun filled room designed to suit your life-style and
budget as well as demonstrating your ecological commitment .
Imagine the comfort in knowing your home is providing you with unsurpassed
security from the elements; tornado's, storms, fires, and intrusion, as well.
The strong, durable materials used in construction means your new home is built to
last generations.
Your home will provide cost and energy savings from the beginning of construction
and throughout the life of your of home.
You will be saving more than enough green house gases to equal driving a
medium size car over 1 million miles.
Our Homes are adaptable to style and are build able in any terrain, soil type and
climate.
Construction time averages two to four days for a basic module with wall and roof.
The energy efficiency of your new Earth Sheltered Home from
Earthlog Custom Homes can save you up to 85 % in heating and cooling.
add a Geothermal System , which can make all heat, cooling and
all of your hot water and you could find you have almost no utility bill.
Add a Solar Power System and you may not have a utility bill.
Make more than you need and the local utility has to by it from you by law.
In the construction, conventional rebar steel is placed within the concrete walls and
dome.
Footings are poured, then forms used to create the side walls and domes are set
into place and tied with steel.
Desired door and window forms are placed followed by plumbing and electrical
openings within the walls and ceilings.
Concrete is then poured in one continuous, monolithic pour using a unique forming
system.
After curing, these forms are removed and moved into place for the next module pour.
Each module is keyed and tied together with steel.
Electrical, plumbing an heating systems are typically placed under the floor before
it is poured by your contractor.
Floor slabs and interior partition walls are placed to Blue Print requirements after
the desired modules are completed.
Exterior doors and windows are framed in after floor in poured.
Waterproofing, drainage and insulation is completed to plan specifications as
weather permits.
The basic structure is a 24 foot [ 675 square feet first one, there after 640
square feet because of a common shared wall ] or a 28 foot [ 900 square feet
first one, there after 875square feet because of a common shared wall ] concrete
module with a domed ceiling rising to 13 feet & 1/2 feet.
The Domed roof provides a load bearing capacity a much as 20 times greater than
that of a flat roof.
The perimeter walls are typically 8 feet tall and made of 10” inch thick reinforced
concrete.
{ wall extensions , 20 inches and 36 inches are available as an Options}.
Openings may be placed anywhere within the ceiling and walls.
Modules are joined to each other with any desired openings, including large archways.
Interior walls are usually standard wood or metal studs and moisture resistance
drywall that is now available at any lowes or home depot.
We recommend using materials natural to the area such as natural stone,
brick, tile, wood or plaster.
The design possibilities are limitless.
You can design your home to provide privacy and yet give it a feel of spaciousness.
Any architectural preferences are possible, including Spanish, Colonial, Tudor,
Craftsman, contemporary or rustic log or log siding, northern white cedar, pine,
your choice, add a side or back entrance and have a screened porch.
1. Clean all stumps, trees, and debris and square up the excavation for the house
location. Allow 4 to 6 feet over dig from the outside face of concrete wall to the face of
excavation. By using a transit, determine the finish level of the house on the job site
location. If at all possible, face house in a southerly direction.
2. Trenches carried deeper tan required by plans hall be filled with concrete. In no
case shall fillings under foundations or footings be done with earth. Bottom of
excavations shall be made level and kept free of rubbish.
3. Excavation for footings and trenches may be cut accurate size and side forms
omitted if concrete is poured in cleaned out trenches without cave-ins. Excavate for
utilities, water, sewage, electric, heating plenum, Geothermal coil and transit
ductwork. Protect bottoms of excavations from frost. Do not place foundations,
footings or slabs on frozen ground.
4. Where any indoor pool is planned, that excavation will occur after the house
excavation .
5. Site should be excavated level 14” below top of finished floor height.
1. Perimeter Drain : Install a 4” perimeter drain of 4” perforated holes or 4” flexible
drain tile down on a bed of fresh stone. The drain shall run around perimeter of house
and should be able to free gravity drain on each side of house. Back fill with 4” - 12”
medium size clean stone over perforated pipe with minimum of 4” straw over stone.
2. Crushed Stones : Where percolation is needed apply crushed , washed ¾” stone as
follows.
a. Under floor slab 10” thickness or to top of footings.
b. 4” under perforated drain tile located at the lowest point out to grade.
c. Under furnace plenum, 4” minimum thickness.
These stone areas must be drained back to perimeter drains specified above.
NOTE : It is essential that the supply ducts and plenum be kept absolutely dry for
heating economy.
3. When house is waterproofed, insulated and all utilities in place, back-fill with a
clean material [ don’t use large rocks, lumber, stumps, debris, etc ] This could cause
a break in the waterproofing membrane.
4. Earth cover over roof to consist of 2’ to 6’ of earth minimum and sloping from
center of house to the perimeter exterior walls. Take care not to crush insulation.
Utilize machinery up to 955 loader for backfilling upon fully cured concrete { 30 days
}.
NOTE : The superimposed design load of 327 lb. per square foot has included an auto
live load of 50 lb. per square foot.
Do NOT over load the concrete roof deck with heavy machinery.
We are released of all liabilities if these directions are not followed.
1. Footings : All footings shall be reinforced steel as indicated on plans.All footings
are to be cut in line and grade on undisturbed earth using 3500# concrete 3” slump.
2. Walls : To be cast of 4000# concrete and a minimum of 5 ¼ bag mix, ¾ aggregate
with air entrained. With Fiber Glass/Mix added for Superior Strength.
a. Walls are all 10” thick and 8’ high, unless you have added wall extensions
as an option with #4 bar at 12’ x 12’ centers each way, 3” from inside wall.
Place all vent pipes, chimneys, utilities in walls or roof.
b. Where needed, electrical outlets with ¾” PVC conduits are placed in wall
before pour and front covered with tape.
3. Roof : Roof is same mix as walls with rebar placed according to specifications.
Walls, roof and overhang of each module are poured at one time [ monolithic pour ]
using our special form systems.
4. Floors: Is the same concrete mix as walls and roof, 4” thick. Vapor barrier of
4-mil polyethylene is under slab. Finish with a steel trowel.
1. Conduit : PVC plastic conduit shall be used in wall. Plastic conduit to be used
under floor. Provide suitable type lock nuts, bushings, couplings, etc. for use with
conduit to make rigid connection between conduit boxes.
2. Wires : Wire shall be moisture proof for underground. No wire smaller than
No. 12 shall be used and where length of run would cause voltage drop of more
than 2% in size No. 10 wire shall be used. Wires shall be different colors to
identify the various lines. Where Romex cable is used with metal studs, use a
plastic grommet to protect wiring from metal studs. MC cable can be utilized
without grommets with a grounding
screw.
3. Outlets : Outlet boxes and covers shall be galvanized.For concrete work the
boxes shall be selected to facilitate electrical work and minimize interference with
placing of reinforcing steel provide galvanized utility and gang boxes for switches.
Conduit and outlet boxes in concrete masonry shall beinstalled as work progresses
and shall not be cut in later.
4. Cleaning : All fixtures, panel boards, motors and all other heating, ventilating
or
electrical equipment furnished or installed by the contractor shall be thoroughly
cleaned prior to leaving the job.
5. Access Panels : The Electrical contractor shall furnish to the general contractor
for installation access panels as required for proper access to any junction boxes.
6. Receptacles : Receptacles to be heavy duty, grounding type, flush duplex 20
amperes, 120 volts. Mount all receptacles in horizontal position unless specifically
noted otherwise. Out door receptacles to be weatherproofed, complete with duplex
grounding type receptacle and double stainless steel gasket cover.
7. Electrical Service : 200 ampere to 100 ampere, depending on size of house. 240 volt,
60 cycle single-phase underground service with outside meter mounted on tub post or
above entry vestibule.
8. Stove, Refrigerator, Dish Washer, Washer and Dryer : Dryers vented through roof
next to pluming vent or out the front of building under floor slab. The five
items listed will be furnished by owner and installed by your contractor.
9. Air Exhaust : In bathrooms, use Nutone Model, air delivery 70 c.f.m. at .10 SP,
Sound level 3.5 Sones. Mount in drop in ceiling. E-Heating And Air Conditioning
Heating unit can be Electric, Gas, LP Natural Gas must be vented for safety, oil,
wood & Geothermal. An air exchange system MUST be installed, can be added to
heat pump , other heater, Must have it operational in combination with Geothermal
for Efficiency and Safety.You can also heat with airtight wood stove or fireplace.
All units except electrical need combustion air line. An air exchange system
MUST be installed, for Efficiency and Safety.
A. Plenum : To be cast into floor construction or heating coil check with HVAC
contractor for details of your home.
B. Ductwork :
C. PVC pipe for sizes shown on plans.
D. Shall be constructed entirely of PVC plastic for sizes on plans.
See drawing for detain and specifications from HVCA contractor.
All plumbing fixtures, drains, valves, etc. shown on the plans shall be
connected, completed with necessary supplies, waste and vents, whether or not the
roughing in or piping is shown or indicated.
1. Cleaning : All plumbing fixtures, metal, trim, drain, fittings and connections
shall be thoroughly cleaned and left ready for service for the home buyer.
2. Guarantee : The Buyers Contractor, by accepting these plans and specifications,
and signing the contract to finish off the home for the client shall guarantee the
following :
All Equipment, materials and workmanship against all defects in material and
workmanship for a period of one year from final acceptance. To Guarantee that all
work is to be done in a Timely Basis.
3. Flashing : provide flashing for floor drains in waterproofed floor. Fasten flashing
to drain clamp device and make watertight.
4. Clean Outs : Furnish and install clean outs as indicated on the plans or even if not
shown as required according to local and state codes
5. Sewers : Lay piping true to line and grade. Fit ends together and match so that
sewer will have a smooth and uniform invert throughout its length. Unless otherwise
indicated or directed, maintain 30” minimum cover above piping. Pipe shall be
provided with firm support. Follow local codes.
6. Ordinances and Permits : The owner shall obtain and pay for all permits required
for installation and inspection as required by the existing ordinances. All work shall
conform to state and local codes.
7. Water Service : The plumbing contractor shall arrange with the local water
department and pay for the installation of a domestic water supply service.
The water meter and installation of same shall be included in the plumbing contract.
NOTE :Water company may require that client apply for service.
8. Fixtures : The following list to be supplied by owner or plumbing contractor :
a. Tub/Shower
b. Lavatory
c. Toilet and accessories
d. Kitchen sink , Range, Refrigerator, Cabinets
e. Hot Water heater, unless using direct fast hot water or
Geothermal heating for hot water supply. G-Fireplaces and Chimneys
f. Solar System Design & Installation.
1. The fireplace shall be a heatilator type stove using a vent from house air handler
unit to circulate around firebox and act as a natural heatilator.
2. All freestanding wood-burning fireplaces as indicated on plans shall be furnished at
owners request and cost.
3. The chimney shall be a clay flue line or metal piping recommended by
manufacturer. Cap all chimneys for water protection. Install spark arrestor.
4. Outside air source must be placed under floor for all fireplaces or wood stoves.
1. The waterproofing membrane is a tar modified polyurethane elastomer. It is
applied as a liquid and forms a bonded synthetic rubber membrane. The material
can be applied with a brush or roller or can be sprayed to the thickness of 1/16 inch.
This permanent bond will prevent travel of water below the membrane even if the
membrane is punctured. The elastic properties our special mix will permit the
membrane to span ordinary shrinkage cracks up to 1/16 inch.
2. A Benoite sheet good material is used in conjunction with rubber membrane on
overhangs,,parapet walls and cold joints.
1. Two 1” layers of 1” x 4’ x 8’ Styrofoam placed directly over top of structure with
offset joints.
2. One 1” layer of Styrofoam placed over vertical walls.
3. One 2” x 4’ x 8’ extruded Styrofoam placed over exterior walls or 3” x 4’ x 8’
expanded polystyrene.
4. Parapets and overhangs require 1” x 4’ x 8’ extruded or 2” x 4’ x 8’ expanded.
1. All metal or wood studs to be 3-5/8” wall stud. Shot top and bottom metal plate into
concrete with ramset gun at 24” o.c. or useconcrete nail or tapcon screw.
2. Place metal or wooded studs 16” o.c. as detailed in plans.
3. All wood sill plates should e pressure treated. K-Drywall . All walls using drywall in
clients plans should use moister resistant drywall availablethrough Home Depot &
Lowes. ½” fire code drywall if code requires. Painted with 2 coats smooth and all
ceilings with one coat sprayed acoustic and or 1 coat flat latex paint over splatter
finish. Fasten drywall to metal stud with 1-1/4“ long screws at 12” o L-Outside Finish
. All walls exposed to the exterior of the home will have 2” extruded Styrofoam
insulation or 3” expanded Styrofoam insulation. Finishes over insulation include the
following :
a. Synthetic Stucco
b. Conventional Stucco
c. Stone
d. Siding
e. Log or Log siding
f. River rock, artificial stone, brick , M-Interior Finishes
g. Interior Concrete walls to be coated with plaster material
h. [ recommend a perlited gypsum plaster called Stuctolite manufactured by US
Gypsum]. Also a skin coat of drywall compound will be applied to make a smooth
surf textured and painted by owner or owners contractor.
1. Door and Door Frames : Standard 4-1/2” prehung and pre-finished doors and
frames to be selected by the owner.
2. Garage Door : To be selected by owner. See plans for size and location.
3. Sliding Glass Doors : If specified on plans, contractor will furnish thermo-pane
glass door.
4. Kitchen and Vanity Cabinets : Pattern to be selected by owner.
Kitchen wall typically furred out to allow for electrical and plumbing requirements.
5. Plastic Laminate Counter : Kitchen and vanity shall be pressure laminate self-
edged on a base of flake board. Kitchen backsplash same material applies to wall
board and underside of cabinets. Vanity backs and end splashes 4” high self-edged as
for counter top or other materials and style and material selected by owners.
1. Carpet with ½” pad.
2. Tile
3. Vinyl Flooring
4. Laminate floating floor system
5. Real Wood floating floor system
6. Stone/ Half Bricks & Mortar
7. Stained concrete
8. Stamped concrete
9. Synthetic decorative concrete
Disclaimer
Purchaser will and shall indemnify and hold harmless this company and its officers,
agents and employees from any and all claims, actions, suits, cost, expenses, damages
and liabilities, including attorney fees, arising out of, connected with or resulting
directly or indirectly from relianceupon and use of plans, drawings and specifications
sold by this company or relating to any negligent act or claim of negligent act thereby
It is expressly agreed and made condition of the sale of these plans, drawing and
specification that this company has attempted to prepare such with care for accuracy
and detail, no warranty, either express, nor implied, is given, nor is it to be construed
nor imposed as to the accuracy or sufficiency of such plans, drawings and
specifications.
The Purchaser is using the same shall and will check all dimensions and other details
and, unless the construction is performed by Earthlog or its sub-contraction of
contracts shall be solely responsible.
Earthlog Equity Group is the ONLY Green Earth Sheltered Home Company that
Offers as Standard OUR LIFETIME WARRANTY on OUR homes from any leakage ,
written into Your Purchase Contract.
*** Full Service Contracts Only ***
Although we have NEVER had a leak in Our Earth Sheltered, Underground or
Earthlog Homes.
Earthlog will repair any leaks that occur in the Lifetime of the Original Purchaser's.
Transferable to your Heirs or a Buyer of your home for a nominal fee.
Our Homes & Commercial Structures are available Nationwide in US, Canada &
Australia.
Download Your FREE 2010 Earthlog Plan PDF Contains 41 Pages of Plans
Click here to Start Download
Slower download or dial up Download the above as 2 parts A & B Below
Earthlog PDF File A Earthlog PDF File B
Your Custom Designed Earth Sheltered Home is Built solid using
fiber-glass/Mix concrete with rebar, ready to stand up to the flying debris of
Tornados and Hurricanes and the devastating effects of Fires and Earthquakes.
Plus, the Superior Energy Efficiency and Soundproofing Qualities of an
Earthlog Earth Sheltered Home means greater comfort for your family
year round.
All of the benefits of concrete home building with architectural beauty.
Beautiful Earth Sheltered Homes in any style with all the added benefits like
Energy Efficiency, Safety, and Peace and Quiet.
Sunken Living Rooms Bedrooms, Indoor Swimming Pools, a Front like a Castle,
or you can even Incorporate a Green House in your overall design.
Larger Homes can have a rear or Side Entrance that can be Designed just as
Elaborate as the Front Entrance or Comfortable the way you want it to be.
A Side or Back Entrance can have a log home look with screened in or Open Porch.
Literally just about anything you can think of can be Designed into the overall Design
of your Custom Designed Earth Sheltered or Underground Home.
Would you like to live or work in a place where:
• you're safe from fire, tornadoes, hurricanes and earthquakes.
• you have very low maintenance costs.
• you have a wide open spacious atmosphere.
• you are environmentally sound.
• you will save as much as 85% on your energy costs with Our Homes,
but that can reduced to a lower amount, or none at all with added
Energy Efficient Green Systems to Create that Special Home.
www.EarthShelteredHousing.com ® Copyrighted 2001-2010
www.EarthShelteredHousing.org ® Copyrighted 2001-2010
www.EarthShelteredHomes.org ® Copyrighted 2001-2010
www.UnderGroundHousing.org ® Copyrighted 2001-2010
www.UnderGroundHomes.org ® Copyrighted 2001 2010
Earthlog Custom Homes® Copyrighted 1989-2010
Earthlog Homes® Copyrighted 1989 -2010
Earthlog® Copyrighted 1989-2010
Earthlog Equity Group® Copyrighted 1989-2010
Earthlog Financial® Corporation Copyri
Earthlog Equity Group Earth Sheltered Building Systems
Your Source for Earth Sheltered & Underground Homes
" Energy & Cost savings, a combined Benefit "
D - Electrical Work
C - Concrete Work
A - Excavation and Grading
B - Drainage and Stone Work
E - Plumbing
F - Waterproofing
G - Insulation
H - Steel or Wood Studs
I - Carpentry
J - Flooring Choice over Concrete Floors
Blue Print Fees are rebated, that is they are subtracted from Total when Your Home is Ordered
Would you like to live or work in a place where :
* you're safe from fire, tornadoes, hurricanes and earthquakes
* you have very low maintenance costs
* you have a wide open spacious atmosphere
* you are environmentally sound
* you will save as much as 85% on your Energy Cost with Our Homes
* that can be reduced to a lower amount with added Energy Efficient Green
Systems to Create that Special Home.
Earth Sheltered Inns ® International Copyrighted 1989 - 2012
Earthlog Custom Homes® Copyrighted 1989 - 2012
Earthlog Homes® Copyrighted 1989 - 2012
Earthlog Equity Group® Copyrighted 1989 - 2012
Earthlog Financial Corporation® Copyrighted 1989 - 2012
EarthlogTek® Copyrighted 2003 - 2012
Earthlog News® Copyrighted 1989 - 2012
Earthlog Energy Corporation® Copyrighted 2001 - 2012
All Rights Reserved by Earthlog Equity Group®
Our Email address is [email protected]